This article is a guest contribution by Tangent Works and first appeared on their website. Keyrus and Tangent Works are in a partnership with the goal of making forecasting and anomaly detection more accessible.
AI driven technology is becoming more important in different aspects of manufacturing. Think of applications such as predictive maintenance, quality control solutions, downtime and operational efficiency across the factory floor and supply chain.
The manufacturing world has no lack of challenges: global competition, job shortage, increasing cost pressure, the urgent need to produce better products and to market them faster. The industry is beginning to realize the importance of AI and the adoption of advanced analytic applications such as anomaly detection, real-time quality assurance and supply chain optimization. Deloitte recently reported in a study on the adoption of AI in manufacturing that 93 percent of companies believe it will be a critical technology to drive growth and innovation in the industry.
Predictive Analytics is seen more as an effective solution for tackling production pain points. This AI-powered technique uses historical and real-time data to predict critical future outcomes, reduce risk, improve operations, reduce costs and increase revenue.
Gartner defines Predictive Analytics (PA) as a form of advanced analysis of data that examines the question “What might happen?”. Manufacturers can rely on PA for greater flexibility, deeper insights, and faster, more accurate decision-making.
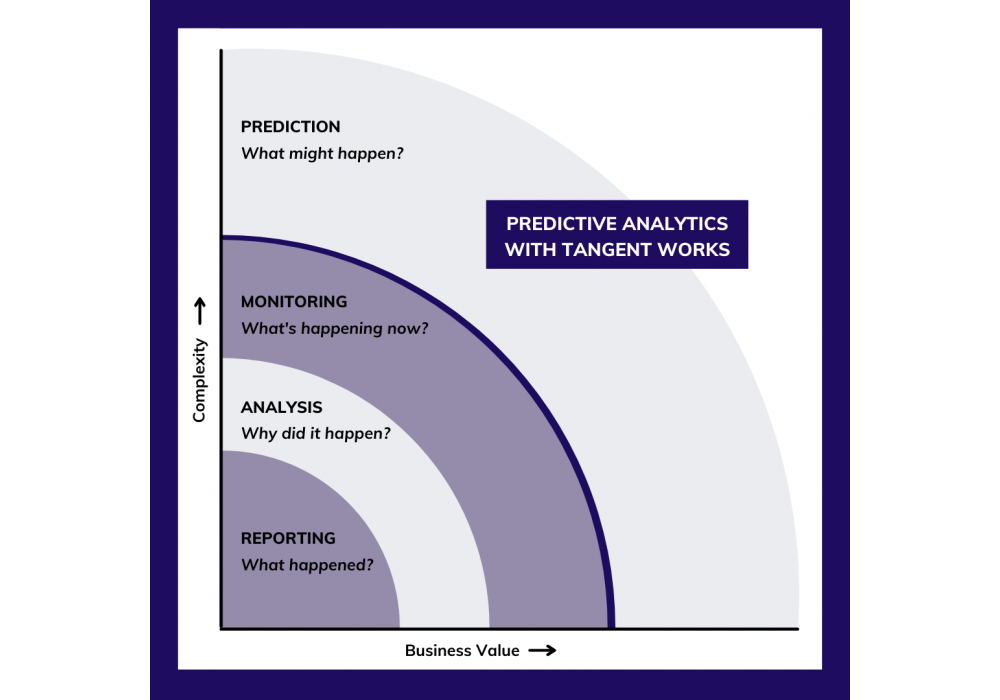
But how to get started?
While PA can bring dramatic benefits to the manufacturing industry, implementing PA techniques in a manufacturing environment can be challenging for various reasons.
First of all, the standard workflow for predictive analytics based on AI and ML is complex and labor-intensive, with long lead times. A typical project involves data preparation, feature engineering, algorithm selection, model training, testing and implementation, and can take anywhere from 6-9 months to complete.
Obtaining quality data in a manufacturing environment is very difficult because each production site can have multiple ERP and execution systems. With dissimilar systems, cleaning and merging data, building functions, and manually generating models can become tedious, expensive and labor-intensive. By the time you do training and validation, chances are AI / ML models are outdated.
Smart manufacturing requires real-time forecasting capabilities for use cases such as inventory management for just-in-time production, quality assurance, and anomaly detection. But how can you create models that provide you with real-time forecasts? Meet InstantML!
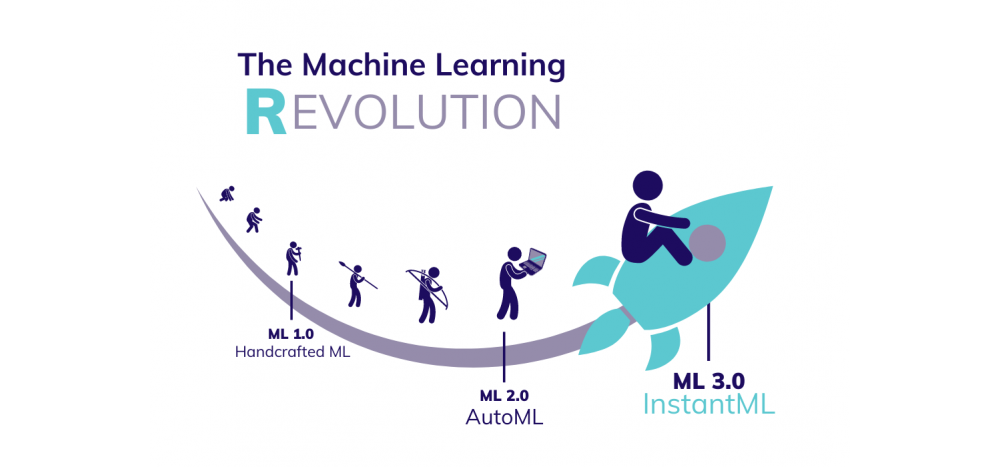
InstantML: create predictive models in seconds
ML 1.0 – Handcrafted models
Often, data scientists create handcrafted models that are used to assist companies with their analysing needs. In crafting these models, they go through a drawn-out processes of data preparation, model building, model deployment and execution. It quickly becomes apparent that this is a laborious and challenging task, and while results may be good, they are not scalable.
ML 2.0 – AutoML
AutoML techniques, which train many different models and then select the most successful out of them. While this is a huge step towards automation, tedious, manual feature engineering is still required, which calls for the input of a domain expert. The result is a compute-intensive trial- and-error process that can take up weeks of valuable time.
ML 3.0 – InstantML
Tangent Works has developed an automatic model-building engine for time-series forecasting and anomaly detection, called TIM. TIM goes beyond these methods with its InstantML technology. With InstantML, a model is created in one single step, including feature engineering, model building and model deployment. All of this these steps are automated and happens under the hood of the TIM engine. The user provides input data, and TIM returns one unique model, that can be used for the specific forecasting and anomaly detection use case.
ML 4.0 – RTInstantML
With the unique RTInstantML technology, TIM goes even further. RTInstantML automates everything from model building to model application, taking input data and directly providing the user with the relevant forecast. This phenome eliminates the need to set up a particular data availability situation, as the forecast can be extracted directly from the input dataset at the time of forecasting. The user only needs to specify how many steps ahead the forecast should be calculated by TIM.
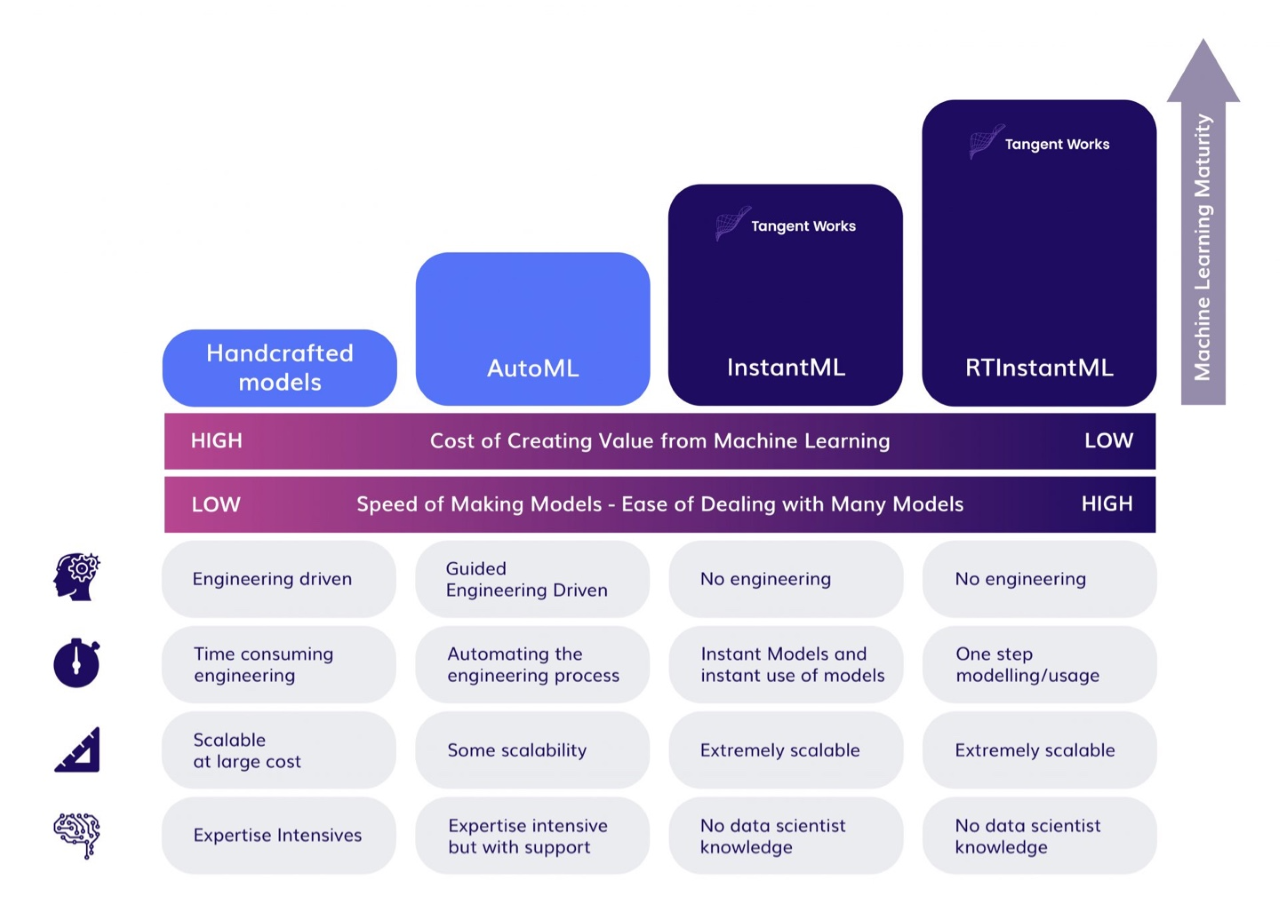
Conclusion
Few industries can benefit more from predictive analytics than manufacturing. The industry generates massive amounts of data, involves repetitive manual tasks, and presents multidimensional problems beyond the reach of many conventional tools. Whether it’s improving quality, reducing downtime or optimizing efficiency, AI-driven predictive analytics is the perfect technique to solve many complex production problems. With our TIM Engine for time-series forecasting and anomaly detection, we enable you to create accurate predictive models in seconds.
Part of this text is based on information from www.manufacturing.net.
Check out the original article and a lot more on the blog of Tangent Works.