Article publié par Jérémy Fasy, Data Scientist, équipe Data Science & IA chez Keyrus
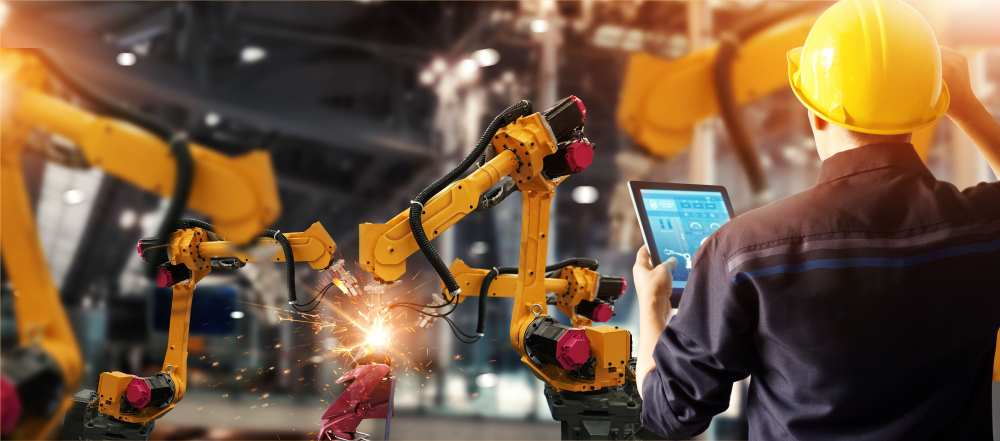
Après une décennie de domination des termes tels que « Connaissance clients » ou encore « Marketing personnalisé », la data s’émancipe et se tourne désormais de plus en plus vers le secteur de l’industrie. Et il faut dire que les sujets ne manquent pas : Quelle est la durée de vie des machines ? Comment optimiser la chaîne de production ? Quand ce composant est-il susceptible de tomber en panne ?
Afin de répondre à ces problématiques, les entreprises n’hésitent pas à adopter une stratégie de maintenance prédictive. Ce domaine de la data a récemment émergé grâce à la combinaison de 3 facteurs clés :
La multiplication des capteurs installés sur les machines qui permettent de collecter de plus en plus de données. C’est ce qu’on appelle l’
IoT
(Internet of Things).
Le fort développement des solutions de
cloud computing
comme AWS ou Microsoft Azure. Ces solutions proposent une multitude de services comme le stockage massif de données et leur analyse. Ces solutions ont l’avantage de pouvoir complètement s’adapter au besoin du client, et les frais engendrés sont calculés en fonction de l’utilisation.
Le Machine Learning, et plus particulièrement le
Deep Learning,
qui permet d’appliquer des méthodes d’apprentissage automatique afin de classifier et prédire des phénomènes tels que des pannes.
Préventive versus prédictive
La maintenance prédictive doit être distinguée de la maintenance préventive. Cette dernière, qui existe depuis de nombreuses années, consiste à mettre en place un planning d’interventions régulières à des périodes prédéfinies. Ces opérations de maintenance peuvent cependant être superflues et générer des coûts qui auraient pu être évités. Elle est par définition plus simple à mettre en œuvre mais sera bien moins pertinente.
La maintenance prédictive a pour objectif principal de prédire quand la panne d’une machine ou d’un équipement peut se produire. Les bénéfices sont nombreux : planification des maintenances avant que la panne se produise, diminution des coûts de maintenance, fiabilité accrue, satisfaction client améliorée. Les chiffres tendent à montrer que la mise en place d’une stratégie de maintenance prédictive permettrait une réduction des coûts de maintenance d’environ 20% et une baisse des pannes de moitié. C’est dans cette optique que les grandes entreprises comme SNCF ou Renault n’hésitent pas à investir dans ce type de stratégie.
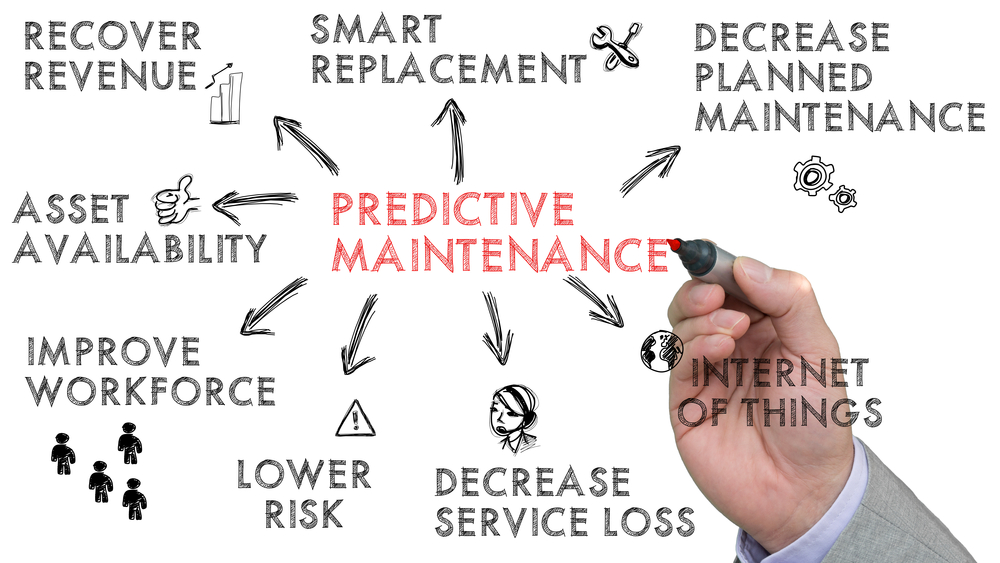
La maintenance prédictive, uniquement des étoiles plein les yeux ?
Comme beaucoup de projets data au premier abord, la maintenance prédictive semble être capable de révolutionner votre service de maintenance et vous faire gagner beaucoup d’argent. Cependant, il faut être lucide et conscient que les belles perspectives promises par la maintenance prédictive s’accompagnent de quelques contraintes.
Tout d’abord, mettre en place une stratégie de maintenance prédictive peut être coûteux. En effet, récupérer et stocker de grandes volumétries de données nécessitent un investissement non négligeable. Ensuite, il ne faut pas s’attendre à avoir des réponses dans les semaines qui suivent. Généralement, plusieurs mois, voire années, sont nécessaires pour appréhender les données, prendre du recul par rapport à ses aprioris, tester des modèles de prédiction et mettre en production ces derniers. Enfin, un point important souvent oublié, est l’implication de ses équipes métiers. À moins que vous ayez le fameux Data Scientist à 5 pattes à la fois expert des données et référent dans votre métier, vous aurez obligatoirement besoin de l’implication de vos équipes métiers pour qu’elles apportent leurs connaissances acquises au cours de leurs années d’expériences dans votre domaine.
Et concrètement ça donne quoi ?
Récemment, un de nos clients a décidé d’amorcer le sujet de maintenance prédictive au sein de son activité. Leader international dans son secteur, ce client a équipé de capteurs une gamme compl ète de ses machines. Les capteurs enregistrent les données de température, pression, courant et d’usages de la machine. Ces données sont envoyées en temps réel dans le cloud. La quantité de données générées est élevée avec plusieurs Go par jour.
Pour ce client, la première priorité a été de connaître comment ses machines étaient utilisées par ses clients. Ce type de sujet est généralement lancé avant d’entamer véritablement un projet de maintenance prédictive. L’avantage de cette étape est qu’elle permet d’avoir une première vision de ses données, ainsi que de s’affranchir de certains aprioris pour être en mesure d’apposer un chiffre clair et précis sur comment sont utilisées les machines. Les plates-formes analytiques telles que Tableau ou Qlik permettent de générer des dashboards simples et dynamiques pour répondre rapidement à ce type de problématique. Outre les données collectées sur les machines, le data lake peut aujourd’hui être enrichi de n’importe quelles autres données en open data ou accessibles à moindre coût. C’est le cas par exemple des données météo : désormais, connaître la température, la vitesse du vent, l’humidité pour un jour donné à n’importe quel point du globe est à la portée de n’importe qui.
Développer un sujet de maintenance prédictive requiert un certain niveau de maturité en data. Si vous possédez une grande quantité de données un minimum structurées, il vous sera alors possible d’appliquer des méthodes de Deep Learning. Ces algorithmes sont généralement plus appropriés en maintenance prédictive que les modèles de Machine Learning, plus classiques, car ils sont plus performants sur de grandes volumétries.
Comme évoqué précédemment, notre client souhaite mettre en place de la maintenance prédictive afin d’anticiper les pannes machines et détecter les paramètres qui sont la cause de certains défauts. Résoudre ce type de problématique requiert des modèles mathématiques plus subtils à rechercher. Il convient donc d’adopter une approche via les réseaux de neurones. Ce sous-domaine de l’intelligence artificielle est de plus en plus répandu et reste encore « mystique » pour ceux qui ne baignent pas continuellement dans la data. Pour imager : un réseau de neurones fonctionne comme notre cerveau quand il prend des décisions, c’est-à-dire que l’information est traitée par plusieurs couches de neurones afin de prendre la décision finale. Par exemple : « je vois cet objet qui a une forme ronde, une couleur rouge et qui est comestible, j’en déduis donc que c’est une pomme ».
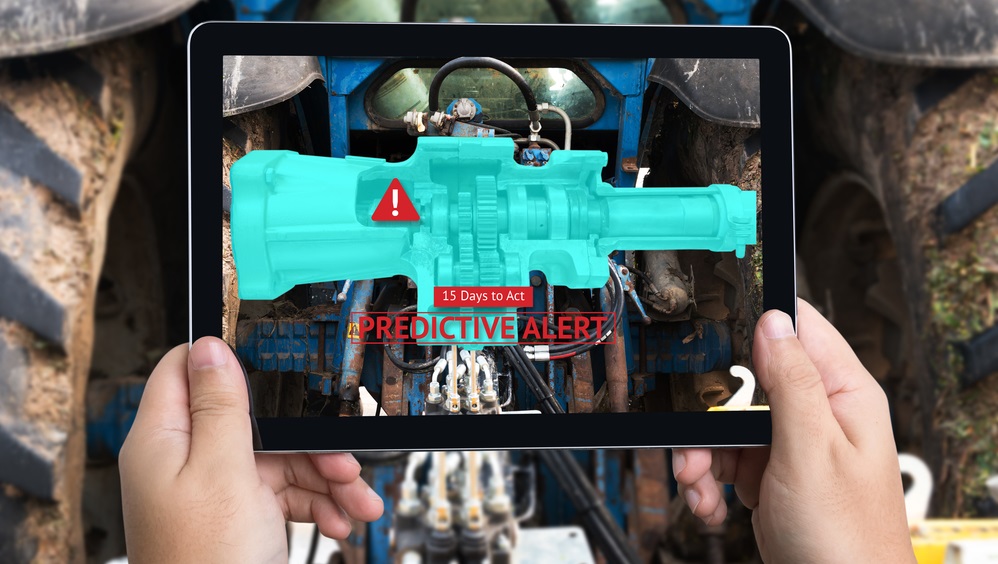
Les réseaux de neurones récurrents, quèsaco ?
En maintenance prédictive, la notion d’historique des événements est généralement très importante. Par exemple, cette panne s’est produite car la machine a fonctionné 1h de plus que d’habitude, à une température bien plus faible que les dernières semaines, et à une altitude plus élevée que la veille. La panne est donc la conséquence d’une succession d’événements passés.
Pour prendre en compte cet historique, à défaut d’utiliser les réseaux neuronaux convolutifs classiques, il est préférable de se concentrer sur les réseaux de neurones dits « récurrents ». Ce type de réseaux de neurones, et notamment les LSTM (Long-Short Term Memory) permettent de prendre en compte la chronologie des événements passés pour prédire des événements futurs. Les domaines d’application sont nombreux : prédiction de maladies, composition de musiques, reconnaissance de langages. En industrie, et plus particulièrement sur le fonctionnement des robots, il s’agit de traiter des séquences de données. Cette notion de séquence est cruciale et l’architecture des réseaux LSTM, avec notamment la notion de feedback connection, est bien adaptée pour faire des prédictions sur des séries temporelles.
Quelles expectatives pour l’avenir ?
La maintenance prédictive a assurément de beaux jours devant elle. Beaucoup d’entreprises industrielles majeures ont déjà investi dans la maîtrise des données, et d’autres plus petites sont en train de sauter le pas. Cette tendance s’est confirmée lors du salon du Big Data 2019.
L’ère du POC est révolue car les concepts ont été prouvés et éprouvés. Le cloud ne doit plus faire peur car la sécurité et ses impacts sont maîtrisés. L’approche par use case doit être privilégiée et driver le recueil des besoins. L’industrie offre des besoins sans limite, et leur résolution passera assurément par la maîtrise des données et l’IA.
Demain, il existera des chaînes de production dans lesquelles l’activité de chaque composant sera monitorée et capable d’émettre une alerte avant qu’une panne se produise, pour ensuite contacter directement le fournisseur et faire livrer la pièce de remplacement. Imaginer une machine capable de s’auto « re-calibrer » en se basant sur ses propres données d’utilisation et environnementales.
Aujourd’hui, votre CRM reçoit un appel de votre client pour se plaindre d’un problème sur sa machine. Demain ce sera votre CRM qui appellera le client pour l’informer qu’une opération de maintenance aura lieu dans les prochains jours afin d’éviter la panne qui se serait produite la semaine prochaine. Et vous ? Qu’imaginez-vous ?